1. Treatment of cyanide barren liquor in gold mine:
There are more associated metals in ores which mix some other impurity ions, and if the leaching solution is not treated effectively, it will affect the next process. In addition, in the process, some substances should be added, and if it is not handled in time, it will affect the next process. In the process of gold smelting, the added leaching agent sodium cyanide is toxic, and the national wastewater discharge standard is 0.05mg/L, but the amount of barren liquor is 0.1g/L. It is impossible to directly discharge it, but the addition of sodium hypochlorite not only consumes a large amount of medicaments, but also wastes the available cyanogen, which is unqualified. Recycling is normally used, and the excessive times of use generate the cumulative effect of impurity ions, especially copper, zinc, iron, calcium and other factors affecting the leaching of gold and carbon adsorption efficiency. Now the common practice is to add acid and alkali to absorb and recycle cyanide ions and produce metal cyanide precipitations. However, on the one hand, the hydrogen cyanide gas appears in this practice, which is prone to poisoning, and on the other hand, a lot of calcium sulfate slag blocking the pipeline can’t be removed.
-
The membrane separation technology is used to deal with cyanide barren solution, and the selection of appropriate membrane will influence the separation of leached and adsorbed divalet ions or multiple valence ions, and it can also recycle gold, silver and available cyanogens. The membrane technology has the following advantages:
-
Free alkali, cyanide ion and complex gold and silver ions in the cyanide barren solution entering the water production measurement will be recycled in the cyanide process, which not only recycles alkali and cyanide ions to save chemical reagent consumption, but also indirectly recycles about 0.05~0.1g/L of gold and silver in the barren solution to improve gold output efficiency.
-
Free alkali, cyanide ion and complex gold and silver ions in the cyanide barren solution entering the concentrated water measurement are concentrated, which not only separates them from the reused water to improve the effective leaching rate of sodium cyanide and reduce the utilization ratio of sodium cyanide, but also recycles copper, zinc, iron and other cheap metals to increase production efficiency.
-
The process is a physical separation process that does not require the addition of a large amount of precipitants and neutralizers, thereby saving costs. It is expected that the total cost of the saved sulfuric acid, lime and labor reaches 5 yuan/m3.
-
It doesn’t produce hydrogen cyanide gas, so it will not bring toxic substances to human bodies, as well as a lot of precipitates of calcium sulfate and the lime wastes which don’ conduct complete chemical reaction with green environmental protection function.
-
Complex acidification process should convert the acid solution, and then it should add alkali for neutralization, so it is difficult to control. However, the membrane separation is only a filtration process, which has the advantages of easy control, simple operation and automatic operation, thereby greatly improving the processing efficiency.
-
Membrane separation technology devices cover small land areas and have low operating costs. According to the preliminary calculation, the payback period of device investment is about 1 year. There are obvious economic and environmental benefits.
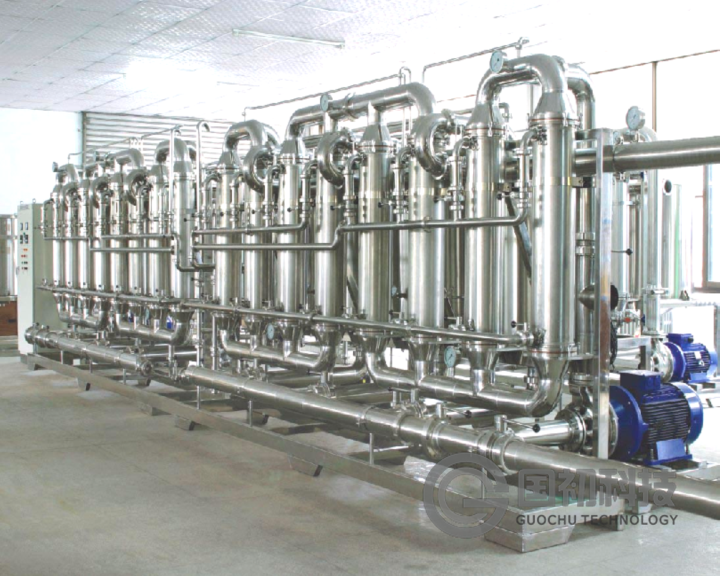
2. Membrane filtration and impurity removal before extraction process
Extraction is an enrichment method often used in hydrometallurgy. However, the emulsification phenomenon and flocculation problem often occur in the process. The reason is that the solid particles and colloidal silica exist less than 1um exist in the leaching solution. The present solution is to regularly extract partial flocculation treatments to recover organic phase. Nevertheless, it will cause partial losses of expensive extractants and increase production costs. Therefore, the fundamental way to reduce floccules is fine filtration.
The particle suspensions and ferrosilicon colloids in the leaching solution affect the extraction process and even produce emulsification and flocculation particles, which not only affects the extraction efficiency, but also causes the loss of expensive extractants and improves the production cost. In the extraction solution SS = 10mg/L.
The removal of suspended particle substances and ferrosilicon colloids in the leaching solution by microfiltration and ultrafiltration is the most widely used method and the most effective and mature process. In particular, the ceramic membrane is suitable for the system because of its excellent properties of acid-alkali resistance and oxidants.
The removal of colloidal silicon, aluminum and iron by the ceramic membrane has been applied in industry and has become an indispensable pretreatment process before nanofiltration and reverse osmosis process.
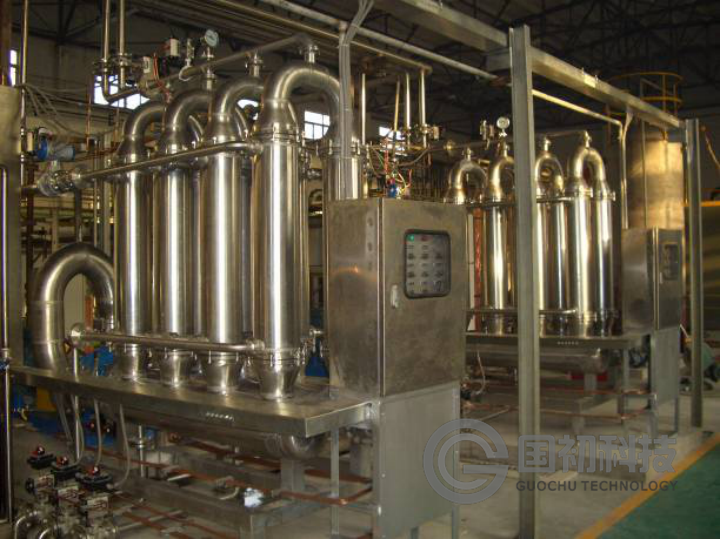
Contact:
Tel:+86 592 6514970
Email:market@guochukeji.com
Skype:18060902001
WhatsApp:18060902001
WeChat:18060902001
TM: guochukeji
QQ:1641011431